Self Audit Checklist
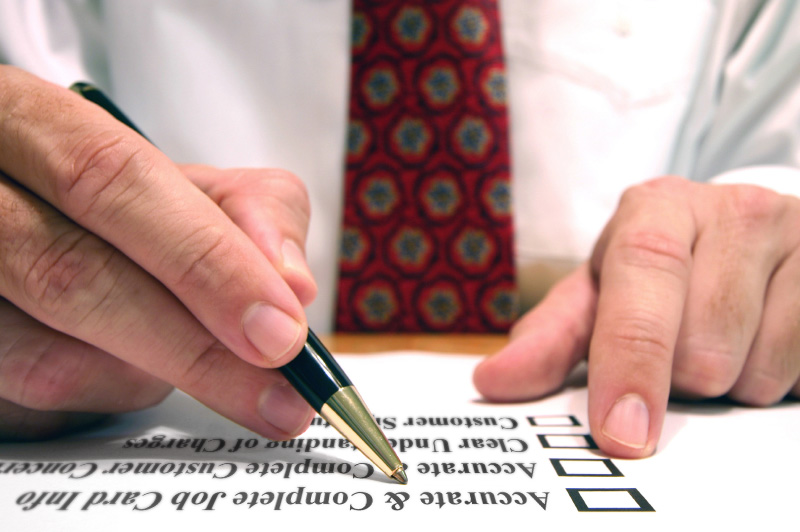
Performing an Internal "Audit Check"
jlwarranty has created the “Self Audit Checklist” so you can personally monitor and check your service department’s warranty job card compliance. These checklists include the primary points that auditors are keying on.
First, you will need to plan a meeting with all personnel involved with warranty. Then, using the “Self Audit Checklist,” personally go through each of the points and note the names of individuals who are ultimately responsible for checking each point. The checklist has been broken down into separate job categories to assist you. On your master copy you should document who is responsible for examining each point and list a follow-up date and action required, if necessary.
Next, randomly pull a few job cards (warranty and shop copies) from the previous month. Inspect each claim against the “Self Audit Checklist.” If one or more checkpoints are violated, the claim could result in a debit during an audit. Look for trends so you can find the root of the problem. For instance, if you are noticing the customer’s signature is not present on job cards, check the service advisor’s number or name on the job card and counsel that individual. Or if you notice that your technicians are not noting the necessary documentation (cause of failure, correction, specifications, etc.), plan a shop meeting to discuss those issues. You may want to have your service manager and warranty administrator present during your review in case you have any questions.
The key is the follow-up. Conduct your “review” monthly or bi-monthly to make sure the appropriate changes are being made. No matter what is found on each review, a meeting should be held (with all service personnel attending) to focus on areas that need improvement and areas that have improved. Don’t expect what you don’t inspect.
Remember, if you have any questions feel free to call jlwarranty (800-852-6298). Don’t wait until it’s too late or you'll be giving your money back to the OEM. The OEMs’ auditors may hand you a large charge back, but they can’t spend much time training you where you went wrong. If you continually “audit check” your service department, you decrease the chances of a large charge back substantially.
Select below:
Service Advisors
All job card header information must be completed accurately, including the service advisor’s number, the in-service date, and the odometer reading taken directly from the vehicle by the person writing the job card. The name and contact information of the owner or operator of the vehicle must be included on the job card.
A clear and concise job card write-up is required with a brief description of each customer concern. Vaguely written complaints such as “engine stalls,” “check brakes,” or “S.O.P. in” are not acceptable. The Complaint is the first C in the 3 C’s (Complaint, Cause, Correction).
There must be a clear understanding of responsibility when the job card is written while the customer is present. Service Management must authorize any changes in responsibility for charges prior to the work being preformed. The customer must be called prior to performing any additional work if there are any additional charges.
A customer’s signature must be obtained to authorize customer pay and/or warranty repairs. If the customer’s signature cannot be obtained when the job card is written, a signed authorization must be attached, or there must be a clear explanation of why the signature was not obtained along with the Service Manager’s signature.
Courtesy Transportation is to be provided for safety concerns, scheduling conflicts, or when a repair requires more then one business day, and/or as prescribed by the specific OEM policy. The number of rental days or alternate transportation must be substantiated by job card documentation. A copy of the rental invoice must be attached to the warranty copy.
Vehicles must only be towed for a safety concern or breakdown due to warranted failure. Vehicles must be towed to the nearest franchised dealership. Follow required documentation.
Service Managers
The Service Manager must sign for vehicles in dealer inventory prior to the work being performed. This includes all sales inventory, the part’s truck, courtesy van, demos, loaners, and new vehicles during the pre-delivery inspection process.
If a technician requires additional labor hours, the Service Manager must authorize the repair. Service Management must note the reason the time was needed, sign, and date. The technician’s comments must substantiate the additional time claimed. The time must be time recorded separately.
Any repairs that are added after the initial job card write-up (add-on repair) must be approved by the Service Manager prior to the repair being performed. All additional repairs must be approved by the Service Management whether they are newly discovered complaints or multiple repairs to fix one customer complaint. Some OEMs require that customers be notified prior to the repair and/or approve completed work with a signature.
Anytime a customer is reimbursed for a repair, the original repair invoice must be obtained. Verification of vehicle ownership and reimbursement check number must be documented on the job card.
If a vehicle returns for the repair of the same item and it is due to improper inspection, diagnosis, or workmanship, it is classified as a shop comeback and should not be submitted to warranty. Shop comebacks are highly monitored by OEMs. Legitimate part failure replacements should be approved and a copy of prior job card attached.
All Service Management Approvals or “Self Authorizations” must be signed, dated, and a reason for applying the authorization must be documented. Some OEMs also require documentation of the time of approval or authorization.
Any discounts provided by sublet vendors (including rental agencies) must be passed on to the OEM for all warranty repairs.
If your OEM allows the use of customer concern not duplicated (no problem found), it can only be used in conjunction with a customer originated concern. The technician must document the amount of time required and must be trained in the repair area. Vehicles in dealer inventory are not eligible. The Service Manager must approve all no problem found operations on the repair order prior to claim submission.
Any damage that has occurred to a vehicle prior to its arrival to the dealership is considered transportation damage and must be submitted on a transportation claim with the delivery receipt completed and attached to the warranty copy. Many times transportation damage is missed on delivery and submitted as warranty. These claims are easily spotted by an auditor, such as body work completed on a low mileage vehicle. Verify that your new vehicle check-in person is properly trained and knows OEM policies. We recommend that a back up person also be trained.
OEM analysis reports are usually sent out monthly by the OEM. These reports should be reviewed and analyzed so you can control areas of high expense before the OEM does.
Check to see that the dealership is knowledgeable about which assemblies are allowed by the OEM to be rebuilt. And if so, that a quick cost analysis is performed to determine if an assembly should be replaced or whether it should be repaired.
Warranty Administrator
All labor operations claimed must encompass the whole repair. Labor operations that are used in which multiple repairs overlap each other are not permitted.
If the dealership uses separate repair orders for customer pay and warranty work, they should be cross-referenced if completed on the same repair visit.
Sublet bills must be the same or less than the cost of the repair if it were to be done by the dealership. If the sublet bill is higher, the difference will be charged back during an audit. Therefore, a written estimate should be given to sublet shops showing the cost they will be reimbursed. Sublet bills must be detailed with the same information as required on the dealer job card copies (3 C’s, parts, materials, straight time, etc.).
All sublet bills must be cross-referenced to the job card and should also include the VIN, mileage, owner name, date of repair, and repair detail. The repair order must contain the name of sublet account and the invoice number. A copy of the sublet bill should be attached to the warranty copy of the job card.
All tow bills must be cross-referenced to the job card and should include the vehicle license number, VIN, PO #, location of a pick up, and the number of miles towed. When towing is performed by the dealer, the location from where the vehicle was towed must be recorded on the job card.
All documents must be retained as determined by the OEM for a given period from the repair order date, including customer pay, warranty, internal, and voids. This includes all supporting documentation including sublet bills and all applicable receipts. Time limits may be set during an audit for the retrieval of a certain number of repair orders. Pure electronic job cards must be retrievable by repair order number and VIN.
Technicians
Each technician must note what was found as the cause of the customer’s concern and what was done to correct the concern. The Cause and Correction must be documented to complete the 3 C’s (Complaint, Cause, Correction). The absence of one of the 3 C’s on any line can result in a debit during an audit.
Any repairs performed where the technician diagnosed the vehicle using technical equipment or acquired measurements of any kind (engine diagnostic codes, battery voltage readings) must be documented on the repair order, or a printout of the readings be attached (i.e., alignment spec printouts).
The technician’s number and time ticket with hours paid to the tech for each repair must be clearly shown on the repair order. Some OEMs require separate time or recordings for each repair and measure technician efficiency. Be sure adequate time clocks should be conveniently located in the Service Department.
Any warranty parts replaced must be accompanied by an acknowledgement on the shop copy that the defective part was returned for scrapping, retention, or return.
Techs do not perform warranty work in areas that they are not certified.
Parts Department
Every attempt must be made to obtain original OEM parts for warranty repairs. If non-OEM parts are used, some OEMs require disclosure to the customer in writing. It must be documented on the job card why OEM parts were not used.
Some OEMs require that defective warranty parts be held for OEMs inspection. Any parts listed on a warranty claim that are not in the part scrapping area or made available for inspection/scrapping may result in a complete claim debit. Any parts replacements for missing parts (such as a hub cap) must contain the reason the part is missing. All requested cores must be returned immediately following payment.
If your OEM has a corporate part return program, all parts requested by OEM must be returned within a specific number of days from the request to avoid a claim debit. Fluids must be drained from all parts before shipping. Air bags, batteries, and fuel tanks must never be shipped. The Parts Department should have an exemplary process for returning parts promptly and a thorough method of documentation.
The parts department should enter all “lost sales” into inventory and make notation on job cards when parts are obtained for an outside source. This will help you when your parts purchase records are scrutinized by the OEM.
Other
It is recommended that your service personnel sign an ethics statement.
No white out, black outs or erasures are allowed. Use a single line strike out with correction above and initials of person who made change.
Pull some job cards and check that self-authorization is not misapplied for:
- Out of warranty
- Stock vehicles
- To cover mistakes
- After the fact on rejects
There is a copy machine in the service area so documentation (sublet bills, towing, previous repair orders etc.) can easily be copied and retained.
Service history information (electronic or file copies) is easily retrievable by Service Advisors and is utilized to check for open recalls, warranty blocks, shop comebacks, and to help service merchandise.
OEM Warranty Expense Trend Reports are reviewed with Service Manager on a monthly basis and are kept on file. A file of all OEM communications concerning warranty and audit is maintained.

jlwarranty offers customized, In-dealership Warranty Training for GM service personnel involved in any aspect of warranty transaction processing. Since warranty transactions are an important source of revenue for any dealership, a solid understanding of warranty operations is essential. One of our experienced warranty trainers will help ensure your warranty transactions are properly documented and that you understand all that is allowed to be claimed according to GM Service Policies and Procedures. We can also review your previous warranty transactions for policy deviations and provide recommendations to correct the root cause. Call 800-852-6298.