Bulletin 18-NA-146

A new bulletin was created last month to stress the importance of identifying the correct causal part in warranty repairs and to address the proper labor operation choice in some unique situations.
In most warranty repairs, the causal part is readily identifiable. In the technician’s cause and correction stories, the causal part should be named. If not, the job card should be returned to the technician for clarification. Any time an assembly, such as an engine or transmission, is replaced, the part that caused the need for the replacement must be identified by the technician. When the warranty transaction is submitted to GM, the assembly should not be selected as the causal part. Rather, the part that created the need to replace the assembly should be identified in the causal part number or description field.
Here is another example: A vehicle has an extensive water leak resulting in the carpet being replaced. The repair was a reseal of a body seam. Sealant was used in the repair but since sealant in this scenario is considered a shop supply, it would not be billed out on the job card. The only part billed out is the carpet, which is not the causal part. The causal part description field should state that the carpet was replaced due to the water leak.
Labor operations are also readily identifiable in most repairs. Choosing the labor operation for a repair describes to GM what has failed. Below are some unique situations:
Consequential Damage – When one component fails and damages another component, only the labor operation of the component that failed is submitted for reimbursement of the repairs. The part or parts that were damaged are claimed with a single transaction. OLH is used as necessary to cover the labor for the repair or replacement of the damaged parts. The OLH claimed should not exceed the base time published for the damaged part labor operation and repair overlap should be taken into consideration with time reduced accordingly. Additionally, service management approval requirements for authorization code E on the job card do not apply and the technician does not have to have a separate time recording to support the OLH claimed. Authorization comments, however, are still required and must explain that the parts/labor was a result of consequential damage. The transaction may have to be submitted for GM authorization if the parts or OLH ceiling is beyond Service Agent Empowerment limits.
External Part Causes Assembly Failure – If an assembly must be replaced and the causal part is an external part (radiator failed and coolant mixed with transmission fluid or catalytic converter failed and caused engine damage) you would use the labor operation for the radiator or catalytic converter, not the assembly labor operation. All parts replaced as a result of the failed component must be submitted on the same line in the parts field, including the assembly. When an engine or transmission assembly is being replaced instead of repaired, a Cost Comparison Worksheet is still required (even though the assembly labor operation is not being used). PQC authorization is also still required if your dealership is required to contact the PQC for the applicable assembly. Use OLH to cover additional time to replace the assembly replacement. OLH time should not exceed the standard base time allowed for assembly replacement. Service management authorization on the job card does not apply and separate on/off punch time for the assembly replacement (OLH claimed) is not required.
One Concern but Separate Causes – Occasionally a customer will have just one stated concern, but a technician diagnosis finds more than one problem. Examples include a fluid leak concern with two separate and unrelated issues or a noise in the front end with two different part failures. When two unrelated causes are found contributing to a single complaint, these repairs should be claimed separately in two transactions using the labor operation applicable to each failed (causal) component. A second line must be added to the job card to address the second defective part. As the customer expressed a single complaint, this would not be considered a true add-on repair and does not require service management add on repair approval. It will be flagged as an add on repair in Global Warranty and will be included in your add on repair percentage but does not require the approval a true add on repair does. The transaction may require service management approval as a pyramid repair. It is permissible to approve a pyramid repair after the first reject. This does not waive the responsibility of the service advisor in asking fact finding questions to determine if the customer’s concern is actually two concerns and should be written as such.
© jlwarranty
Article from jlwarranty's Warranty Newsletter
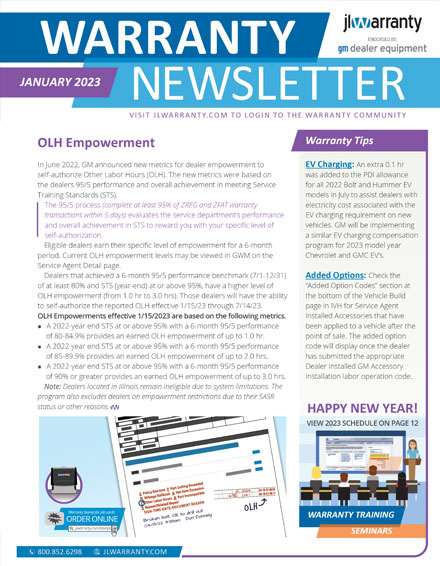
Learn moreTry a 1 Month Trial